Environmentally-assisted degradation
In our society metals are used in a wide variety of applications, ranging from enormous constructions in building and aerospace, to very small units in electronic devices.
Regardless of the application, they always have one common feature, namely that their durability is affected by their interaction with the environment. Often, this interaction, quoted as corrosion, has a detrimental influence on the mechanical, physical and esthetical properties. In the pursuit of increasing the sustainability of metals, a thorough knowledge of this electrochemical behaviour is crucial.
The synergetic effect of sulphate-reducing bacteria and cathodic protection on the hydrogen-induced damage in offshore applications
Offshore structures are exposed to corrosive seawater and should be protected to avoid possibly catastrophic failures. Offshore corrosion protection is usually achieved by combining protective coatings and cathodic protection (CP). However, irregularities in the environment can disturb the CP and cause cathodic overprotection, that promotes hydrogen reduction on the metal’s surface and causes an ingress of elemental hydrogen and, eventually, hydrogen embrittlement. A commonly encountered source of environmental irregularities is presence of microbial life in seawater. Sulphate-reducing bacteria (SRB) are most often associated with corrosion in offshore applications. The synergetic effect of cathodic protection and sulphate-reducing bacteria is still far from understood.
This PhD project deals with hydrogen embrittlement of steels due to the combined action of sulphate-reducing bacteria and cathodic protection. The materials of interest are structural steels, often used for offshore applications. Electrochemical experiments, such as potentiodynamic measurements, and hydrogen related measurements, such as melt/hot extraction and electrochemical hydrogen permeation, are combined with mechanical tests, such as four-point constant extension tests, in environments with combined SRB and CP. The combination of techniques will provide essential insights in the electrochemical reactions taking place and allow to optimise the applicability of these materials for future offshore applications.
Additionally, the effect of offshore environmental parameters on the corrosion rate is assessed. An in-situ sensor system was developed to monitor the evolution of the corrosion rate of submerged steel in seawater. The combination of this data can provide insights in the corrosion risk for offshore applications.
Sustainable corrosion inhibition in open recirculating cooling systems
Elias De Ketelaere, in cooperation with Evides
Cooling water systems are frequently used in industry to control process temperature, as heat is often produced in manufacturing processes. An economic way to reduce the deterioration of the piping in such cooling loops is the usage of corrosion inhibitors. These chemicals are added to the cooling water in order to protect the pipe walls.
In open recirculating cooling systems, every now and then, some amount of cooling water is replaced by an influx of fresh make up water (blowdown). This measure is taken to mitigate the ever-increasing concentration of ions in the cooling system. Consequently, a considerable amount of chemicals, added to inhibit corrosion, also end up in surface waters.
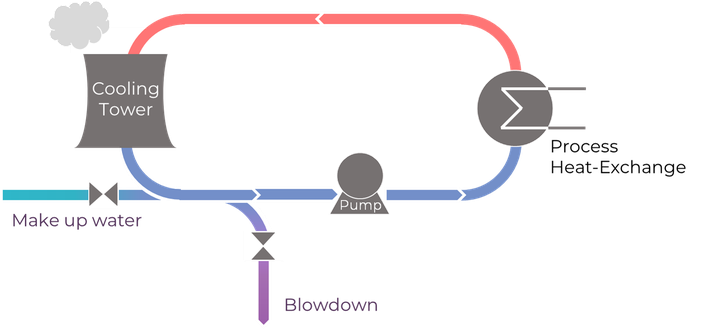
Looking towards a sustainable future, key properties of corrosion inhibitors should include biodegradability and non-toxicity, which rules out popular inhibitors like chromates, nitrates, etc.
In that respect, this PhD research digs deeper on green inhibitors like silicates and film forming amines and their inhibitive functionality, considering the role of key parameters in the aqueous environment such as temperature, pH and flow rate.
Corrosion in sour conditions
Elien Wallaert (interesting papers can be found at the end of this section)
In the oil and gas industry, the presence of H2S gas might induce sulfide stress cracking (SSC). The interaction between steel and the H2S containing surrounding environment also results in the formation of a FexSy corrosion product. Moreover, hydrogen is also generated during this corrosion process and can be absorbed in the material.
It was investigated how the (Mo content of the) base material composition affects the generated corrosion products and their impact on the corrosion rate. The corrosion products that were generated in an aqueous solution saturated with H2S had a two-layered structure. The main composition of both layers was mackinawite (FeS1-x), however they contained different amounts of alloying elements, molybdenum and chromium. This double corrosion layer is illustrated in the schematic below.
Schematic for the proposed mechanism of the double corrosion layer on steel in a sour environment
The upper layer, which was created via a precipitation mechanism, was enriched with Mo. While the inner layer was formed via a uniform corrosion process and was enriched with Mo and Cr. Investigation of the equilibrium phase diagrams for these environments showed the indeed Mo can undergo a deposition reaction, creating MoS2, while Cr will not undergo any deposition but remain in solution as Cr2+.
The presence of this double corrosion layer has a large influence on the amount of diffusible hydrogen in the materials. This amount decreased as a function of contact time with the H2S saturated solution, while the corrosion rate of the materials shows no significant reduction. Therefore, the corrosion products are assumed to act as a physical barrier against hydrogen uptake.
Interesting papers:
Fusion reactor materials (finished project)
Leandro Tanure, in cooperation with SCK-CEN (Concluded, interesting papers can be found at the end of this section)
The study and characterization of Plasma-Facing Materials (PFM) will largely determine the success of future nuclear fusion reactors. These reactors are proposed to replace conventional nuclear power plants (based on nuclear fission) once they are safer, more reliable and produce considerably less nuclear waste.
Nuclear fusion reactions involving hydrogen isotopes require extremely high temperatures (millions °C) which are achieved in the plasma state. The main goal of this research is to understand how plasma exposure affects and changes the microstructure of the most promising PFM: tungsten and tungsten-based alloys.
During fusion loading conditions, PFM are challenged to keep their mechanical properties and microstructural features, as long as possible, under severe requirements such as high temperatures, thermal loads, thermally induced mechanical stresses and neutron irradiation. After plasma exposure experiments, the samples are characterized via Scanning Electron Microscope techniques and Electron Backscatter Diffraction (EBSD). Mechanical behavior is evaluated through nano-indentation and tensile tests.
This project is carried within the framework of Erasmus Mundus FUSION-DC program in close collaboration with the Belgian Nuclear Research Centre (SCK.CEN), Dutch Institute For Fundamental Energy Research (DIFFER) and the Eindhoven University of Technology (TU/e).
Inverse Pole Figure maps (obtained via EBSD) of a forged tungsten sample. (a) annealed at 1000 °C and (b) annealed at 1300 °C.
ND: Normal Direction. BA: Bar Axis. Color code with respect to ND.
Different colors represent a specific orientation of each small grain of the material.
Interesting papers:
- 10.1016/j.surfcoat.2018.01.075
- 10.1016/j.jnucmat.2019.07.005
- 10.1016/j.jmrt.2019.07.015
- 10.1016/j.jnucmat.2020.152201
Stress-corrosion cracking (finished project)
Tim De Seranno (Concluded, interesting papers can be found at the end of this section)
Issues related to the availability of water pushes industry to use alternative water sources. This observation, as well as the use of new water treatment chemicals, often contribute to increasing concentrations of organics in boiler feed water. Under boiler conditions, organic compounds decompose by hydrothermolysis into organic acids, such as formic and acetic acid, and CO2. In low‑pressure steam turbine sections, steam starts to condense and these organic acids concentrate in the first condensate. In this way, the pH of the first condensate is lowered, as such increasing the susceptibility to corrosion, such as stress-corrosion cracking.
In this PhD work, it was shown that higher acetic acid concentrations resulted in increased losses in both strength and ductility of steam turbine steel. Faster failure might have been caused by anodic dissolution and/or hydrogen embrittlement. Furthermore, hydrogen embrittlement was identified as an active mechanism of the formation of stress-corrosion cracks (cf. Figure 1) that initiated after reaching the ultimate tensile strength. Hence, future steam turbine steels might benefit from the introduction of precipitates, e.g. chromium carbides, that have a good hydrogen trapping capacity.
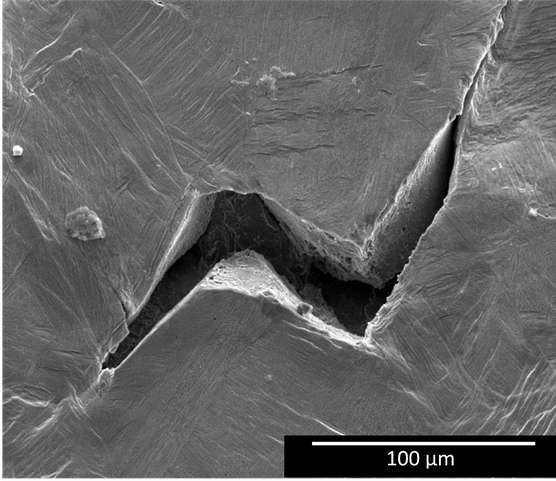
Furthermore, less mechanical degradation in acidic aqueous environment was obtained when steam turbine steel was coated with film forming amines. The corrosion rate increased at higher flow rate and varied depending on the type of organic acid (cf. Figure 2). pH and conductivity appeared to be insufficient in providing guidance for corrosion monitoring. Therefore, the role of the type of organic on corrosion damage is an absolute prerequisite to be incorporated in industrial guidelines of steam-water cycles for safe future electricity production.
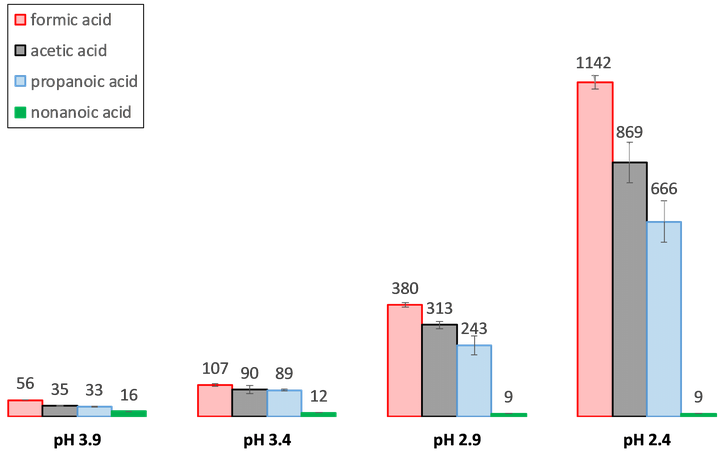
The composition of the acidic aqueous environment was obtained from first condensate sampling in lab scale boiler experiments, performed at the Faculty of Bioscience Engineering (at the Particle and Interfacial Technology Group (PaInT) research group). This project is situated in the framework of the IMPROVED project, which is an INTERREG funded project that aims to build mobile units for water resource recovery in chemical industry.
Interesting papers:
Hot-dip aluminized steel: characterization and evaluation (finished project)
Babs Lemmens, in cooperation with VUB (Concluded, interesting papers can be found at the end of this section)
Steel can be protected against the deteriorative effect of corrosion by applying a metallic coating, for which aluminium is widely used. The metallic coating is most often applied by hot-dip aluminizing. During the dipping of steel in Al interdiffusion occurs, giving rise to the formation of intermetallic phases (IMPs) which are hard and brittle.
In industrial aluminizing processes, Si is commonly added to the Al bath to reduce the thickness of these IMPs. Despite the abundant use of hot-dip aluminizing in industry, little is known about the microstructural build-up and characteristics, electrochemical behavior and mechanical performance of the IMPs formed.
In this research project, steel substrates were dipped in Al baths containing varying amounts of Si for changing times and temperatures. The microstructural build-up of these coatings was investigated using different state of the art electron microscopy techniques. Nanoscale investigations were performed to investigate the location of Si by using atom probe tomography.
The electrochemical behaviour of the hot dip aluminized steel was investigated on both a macroscopic as well as on a microscopic scale, using techniques as scanning vibrating electrode, salt spray testing and gold nanoplating. To fully understand the mechanical performance of Al coatings, standard tensile testing and micro-tensile testing were performed. Some of the results are illustrated in the figures below.
Phase maps of hot-dip aluminzed steel dipped in pure Al (left), Al with 3% Si (middle), Al with 5% Si (top right) and Al with 10% Si (bottom right), obtained via electron backscatter diffraction.
2-dimensional concentration plots of Al (a), Fe (b) and Si (c) of the intermetallic phases, obtained via atom probe tomography.
Evaluating the influence of dipping temperature on the deformation behavior via tensile testing and scanning electron microscopy analysis.
- 10.1016/j.surfcoat.2014.06.064
- 10.1016/j.matchar.2016.09.008
- 10.1016/j.surfcoat.2017.03.040
- 10.1016/j.msea.2017.10.094
Microstructural characteristics of corrosion processes (finished project)
Linsey Lapeire, in cooperation with VUB (Concluded, interesting papers can be found at the end of this section)
In current literature, corrosion is often considered as a purely chemical interaction with nearly exclusive dependence on compositional effects, whilst ignoring the microstructural and crystallographic properties of the metal surface. In this research project it was demonstrated that there is an important correlation between the corrosion behaviour of the metals and the grain orientation, grain size and grain boundaries.
After a controlled variation and thorough characterization of the microstructure of a carefully selected metal, the resulting electrochemical behaviour was meticulously quantified. This was done in close collaboration with the research group SURF at VUB. In this way valuable knowledge was generated for the design of metals with improved corrosion resistance, which is illustrated in the following images.
Gold-nanoplating (right part of image), an in-house developed technique, in combination with electron backscatter diffraction (left and middle part of image) makes is possible to quantify the electrochemical behaviour of grains and grain boundaries.
The combination of scanning electrochemical microscopy and electron backscatter diffraction can distinguish differences in electrochemical activity of the surface.
With atomic force microscopy and electron backscatter diffraction it becomes possible to link the dissolution behaviour with specific crystallographic and microstructural features.
Interesting papers: