Hydrogen-material interaction
Hydrogen interaction with materials typically results in hydrogen assisted or hydrogen induced cracking or embrittlement.
It is well-documented that hydrogen has a detrimental effect on the mechanical properties of steels, especially on their ductility. This phenomenon is designated as hydrogen embrittlement or hydrogen induced cracking.
Even today, this phenomenon is not well understood. Moreover, hydrogen can still induce unpredictable failure of industrially relevant materials, although only a few ppms are present in the metal. Further investigation of the mechanisms that control this phenomenon is therefore essential.
High Strength Steels (HSS) are very prone to hydrogen related failure. Some steels show a ductility loss of 75% when charged with hydrogen! However, these materials are very interesting for the automotive industry and multiple structural applications due to their high strength/stiffness vs. weight ratio.
A detailed evaluation of the interaction between hydrogen and these steels is necessary to understand and predict potential hydrogen damage.
The effect of hydrogen on the fracture toughness of pipeline steels
Margo Cauwels
Hydrogen gas is regarded as key in the energy transition towards a low-carbon economy. Pipeline systems can be used as an economical means for buffering and transporting energy in the form of hydrogen gas. However, a well-known hazard for pipeline steels used for high-pressure transport of hydrogen gas or structural steels subjected to cathodic protection, is ‘hydrogen embrittlement’.
The aim of this project is the development of a methodology and set-up for fracture toughness testing which allows for concurrent cathodic hydrogen charging during the test. Specifically, single edge notch tension (SENT) tests are of interest, because they yield representative values for the fracture toughness of thin walled structures, such as pipelines. This new set-up will be used to perform in-situ SENT test for two pipeline steels, one vintage and one modern steel grade, in order to elucidate the effect of microstructural and -mechanical features on the hydrogen induced degradation of pipeline steels. Moreover, these experiments can contribute to a more general mechanics based damage law for hydrogen induced failure, that is being developed in collaboration with Soete Laboratory.
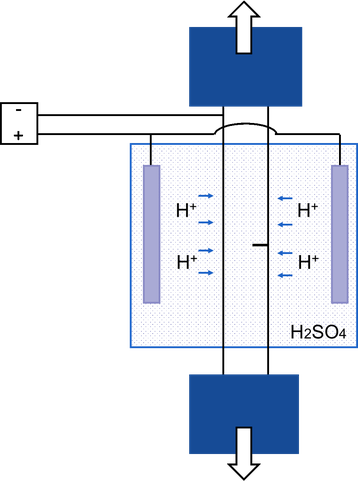
This will be complemented with hydrogen related and microstructural characterization to interpret the mechanical data obtained by SENT testing. Melt extraction will be used to determine the hydrogen saturation level. The hydrogen trapping capacity will be determined by thermal desorption spectroscopy (TDS) allowing for identification of hydrogen traps in the different steels. These traps can then be linked back to microscopic features on fracture surfaces. One such feature typical for hydrogen embrittlement are the so-called ‘fisheyes’ that can appear around inclusions (Figure).

Hydrogen Embrittlement of Advanced High Strength Steels
Simon Vander Vennet
In order to increase passenger safety and reduce vehicle weight and CO2 emissions in automotive applications, it is crucial to obtain an optimal combination of high specific strength and deformability. One of the most promising approaches being investigated is designing a steel which combines a hard phase with a ductile phase, e.g. martensite and austenite. This type of microstructure can be achieved via a Quenching and Partitioning (Q&P) heat treatment. The presence of metastable austenite causes a TRIP-effect, which provides the high ductility of the material, whereas the martensitic matrix provides the necessary strength. Unfortunately, these advanced high strength steels are often quoted to be prone to hydrogen embrittlement.
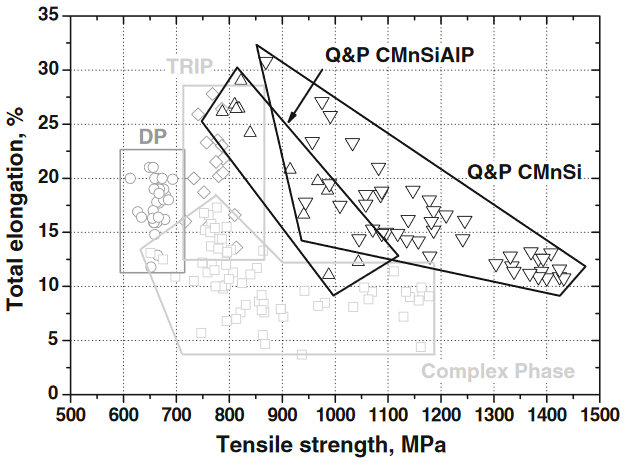
When considering the presence of hydrogen, this combination of phases in Q&P steels may be detrimental due to the large difference in hydrogen solubility between martensite (low solubility) and austenite (high solubility). When the material is deformed, the metastable austenite transforms into martensite. However, due to the high solubility of hydrogen in austenite, the freshly formed martensite is now supersaturated with hydrogen and is therefore more brittle than predicted, causing unexpected and unwanted failure.
The interaction between hydrogen and this two-phase microstructure and its mechanical properties is investigated by means of tensile testing in air and in-situ charged with hydrogen. These tests are carried out until fracture as well as until a certain deformation is reached. This enables us to assess the effect of hydrogen on the TRIP effect at intermediate strains. Additionally, the effect of the austenite-martensite transformation is examined using hydrogen permeation under constant load, combined with subsequent X-Ray diffraction to assess the phase transformation during the permeation test. Constant load tests enable the investigation of cracking in hydrogen-prone microstructural components, as evidenced by the figure below of a welded structure which was kept under constant load during electrochemical hydrogen charging.
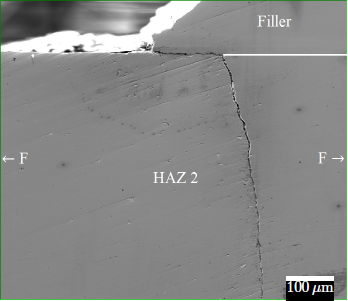
Environmental (hydrogen) assisted failure of titanium
Liesbet Deconinck
Titanium is a comprehensive material due to its high strength-to-weight ratio and high fracture toughness. Furthermore, the spontaneous formation of a passivating oxide layer offers a high corrosion resistance for applications mainly in the aerospace, marine, automotive and biomedical industry. Nevertheless, in reactive environments, titanium is still prone to environmental (hydrogen) assisted failure.
This PhD project aims at investigating aggressive environmental influences on titanium and its alloys (CP grade 2, Ti-6Al-4V, etc.). The relevant types of environmentally assisted cracking include stress corrosion cracking and hydrogen embrittlement. The first category comprises accelerated failure due to the synergistic effect of stress and simultaneous corrosion. The latter type also induces premature failure by the interaction with hydrogen atoms.
The environmentally induced mechanical degradation of titanium is analysed by in situ mechanical tests. Meanwhile, the microstructural response is assessed to evaluate the mechanism responsible for crack initiation and propagation. For this purpose, high resolution characterisation techniques are applied, i.e. optical microscopy, scanning electron microscopy, electron backscatter diffraction, transmission electron microscopy, X-ray diffraction, etc. The left figure illustrates a hydrogen induced crack in titanium during in situ slow strain rate testing. This analysis is combined with a thorough characterisation of the hydrogen properties: amongst others by thermal desorption spectrometry to evaluate the present hydrogen trapping sites, hot & melt extraction to determine respectively the diffusible and total amount of hydrogen in the material, and differential scanning calorimetry to monitor titanium hydride dissociation and phase transitions. The DSC example in the right figure gives an indication of thermal (hydrogen -) material reactions. Furthermore, applications on titanium implant failure in the human body are considered as well.
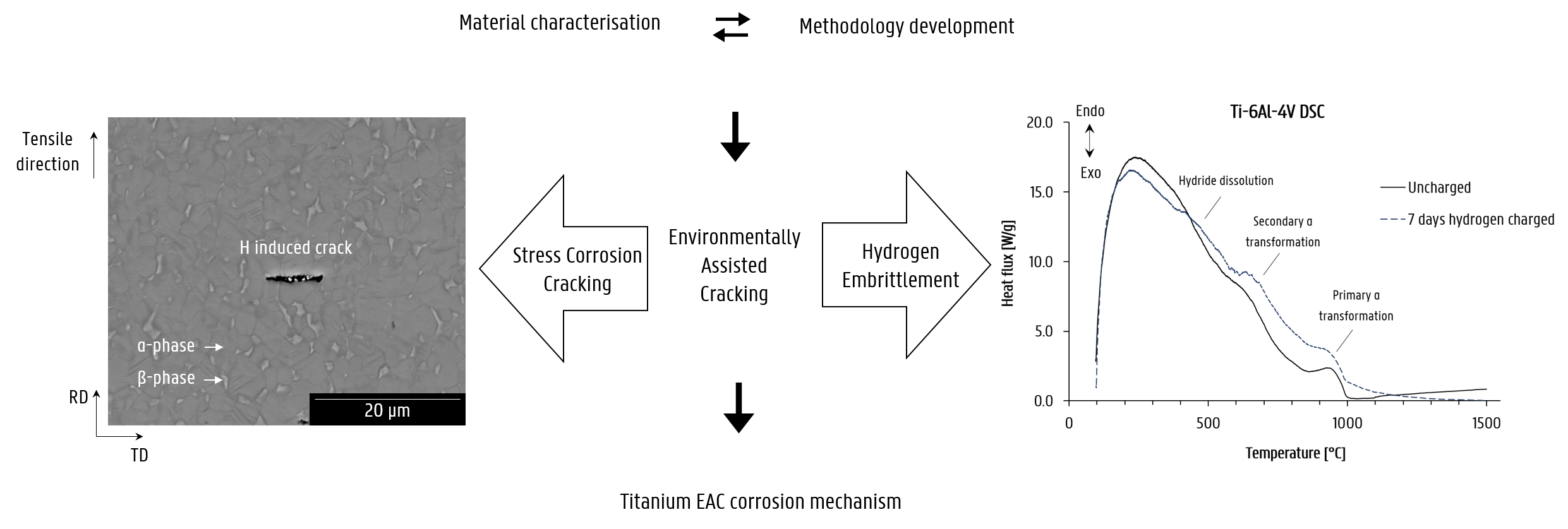
Study of the interactions between hydrogen, carbon and vacancies in iron-based alloys
Liese Vandewalle, in cooperation with SCK-CEN
The interaction of hydrogen with microstructural features can strongly influence the hydrogen embrittlement of a material. Especially the interaction of hydrogen with dislocations and vacancies has been mentioned to play a key role in the hydrogen induced mechanical degradation of steels. However, the interaction of hydrogen with these features is rather complex to study due to their small scale. Furthermore, the influence of the presence of carbon at these features is still unclear as well. Therefore, a novel and innovative approach will be used in this project, i.e. three advanced techniques, thermal desorption spectroscopy, internal friction and positron annihilation spectroscopy, will be combined (cf. Figure). Each of these techniques gives information on a specific aspect of the microstructure and/or the hydrogen interactions and, as such, their combination will aid in gaining a full understanding on the hydrogen interactions with vacancies and dislocations and the influence of carbon therein.
Besides vacancies and dislocations, carbides are also important in terms of hydrogen embrittlement as they have the potential to strongly trap hydrogen and as such remove detrimental diffusible hydrogen from the matrix. Different potential trapping sites are associated with carbides. Nevertheless, for precipitates such as titanium and vanadium carbides, the sites with the highest binding energies for hydrogen are the carbon vacancies inside the carbides. Unfortunately, electrochemical cathodic charging cannot activate these trapping sites due to the high trapping energy barrier. Therefore, in order to study the hydrogen trapping by the carbon vacancies, an alternative hydrogenation method, i.e. gaseous H2 charging, is preferred, while thermal desorption spectroscopy is used to evaluate the trapping ability.
Hydrogen induced damage in lightweight martensitic Fe-Al-C alloys
Margot Pinson
Martensitic steels possess high hardness levels which make them attractive materials for a wide variety of applications. However, due to the increasing environmental issues linked to global warming and CO2 emissions, one of the most urgent challenges is to create lightweight designs to increase the performance and efficiency of machines and transportation systems. Recently, a new alloy concept was introduced by the Max Planck Institute für Eisenforschung (MPIE) based on a Fe-Al-C system which resulted in a light, strong and cost effective martensitic steel which shows a lot of potential, especially for applications requiring high strength and hardness levels.
However, steels used in industry are exposed to hydrogen (H) containing environments both during the production cycle and during their lifetime. Hence, my PhD was introduced in close collaboration with MPIE to investigate the effect of the chemical alloy composition and microstructure on the susceptibility to hydrogen embrittlement of well-designed Fe-Al-C alloys with varying Al and C content. The insights obtained during this PhD aim to contribute to the further development of these promising Fe-Al-C alloys. For this purpose, several high resolution characterization techniques such as Scanning Electron Microscopy (SEM), Electron Backscattered Diffraction (EBSD), Differential Scanning Calorimetry (DSC) as well as several H characterization techniques such as melt extraction and thermal desorption spectroscopy (TDS) are used. Since these ultra-high strength steels are designed for applications where the hardness values are more important than the deformation (e.g. bearing applications), the low ductility hinders the traditional investigation of the degree of hydrogen induced mechanical degradation by H in-situ tensile tests. Therefore, a new in-situ H charging bending technique was developed to investigate the susceptibility to hydrogen embrittlement of high strength steels with limited ductility.
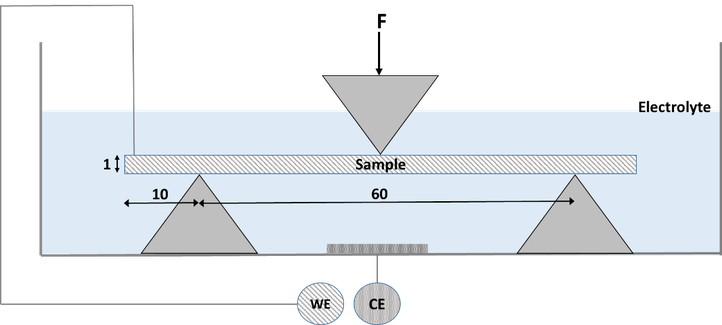
This new technique already allowed to investigate in detail the mechanism of hydrogen embrittlement of generic Fe-C steels with a martensitic structure. It was found that H causes a significant ductility loss, characterized with a transition from a microvoid and/or intergranular fracture surface to a cleavage fracture surface with additional cracking. The transition to the transgranular fracture type is explained by the Hydrogen Enhanced Plasticity Mediated Decohesion model which indicates that hydrogen is preferentially trapped at packet or block boundaries in martensitic Fe-C steels.
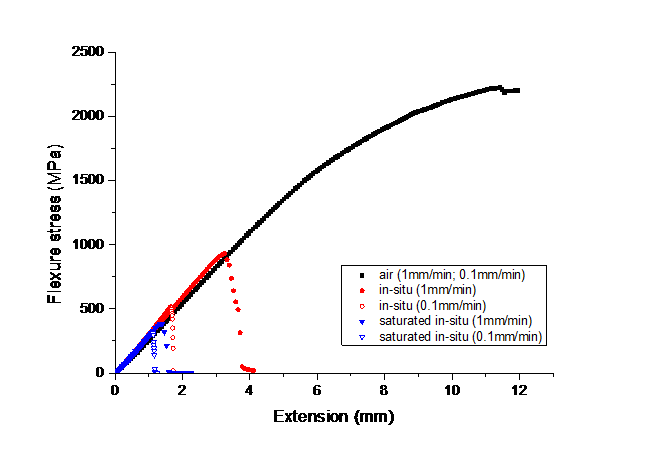
Study of the hydrogen induced degradation of austenitic steels (finished project)
Lisa Claeys, in cooperation with VUB (Concluded, interesting papers can be found at the end of this section)
For a long time, face centered cubic (FCC) steel types were considered insensitive to hydrogen embrittlement because of their intrinsically low hydrogen diffusivity. However, in recent publications, it was shown that FCC steels also suffer from hydrogen embrittlement.
In the first part of this PhD, the interaction between hydrogen and 2205 duplex stainless steel (DSS) was studied. Electrochemical cathodic hydrogen charging of duplex stainless steels resulted in very high hydrogen concentrations (up to 710 wppm at saturation). Moreover, during the charging procedure, slip lines were induced in the austenite phase. An image of this phenomenon is shown below where electrochemical charging lasted for 18 hours.
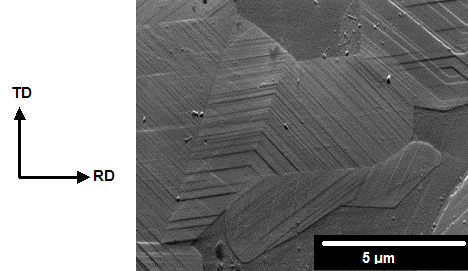
The interaction between hydrogen and the DSS microstructure was investigated with thermal desorption spectroscopy. A model based on Fick’s second law was also constructed. By fitting the model to the experimental data, an effective hydrogen diffusion coefficient for 2205 DSS was obtained: 3x10-7 *exp(-43400/RT) m²/s. The fit to the experimental data can be seen in the image below. Due to the low diffusivity, hydrogen trapping could not be distinguished.
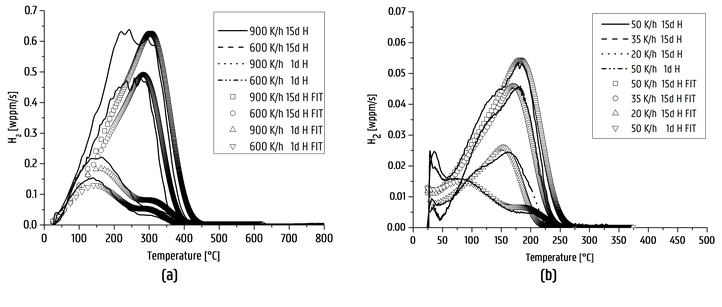
The active deformation mechanisms upon straining of DSS were investigated with electron backscatter diffraction (EBSD) on interrupted (26% strain) constant extension rate tensile test specimens. The initial state is compared to the air tested, ex-situ and in-situ hydrogen tested specimens in the image below. Hydrogen precharging was performed for 1 day. Due to the presence of hydrogen, deformation of austenite became more planar and martensitic transformations took place. Both ε-martensite and α’-martensite were observed due to the reduction of the stacking fault energy and the pinning of edge dislocations by hydrogen.
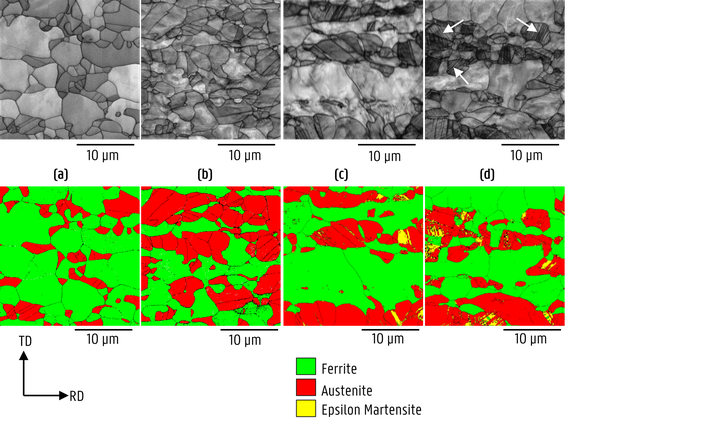
Secondly, the influence of the applied strain rate on the hydrogen embrittlement sensitivity of 304L austenitic stainless steel was investigated. A higher strain rate resulted in less embrittlement due to the limited time for hydrogen diffusion, i.e. diffusible hydrogen is also detrimental in FCC steels. Hydrogen increased the α’-martensite fraction after straining. Moreover, ε-martensite was also observed. The enhanced martensitic transformations (mainly ε-martensite) can be regarded as a positive hydrogen contribution since this increased the ductility. To improve the HE resistance of stainless steel, these transformations should be exploited more in the future.
Finally, the hydrogen embrittlement sensitivity of twinning induced plasticity (TWIP) steels was investigated as well. TWIP steels have a high manganese content (>17 wt%) which causes them to be austenitic (FCC) at room temperature. They combine a high strength with large elongations at fracture and a high energy absorption potential. The properties are a result of twin formation and dynamic strain aging. Owing to these exceptional properties, TWIP steels have a lot of potential for applications in automotive, oil and gas industry. The role of the stacking fault energy in the beneficial effect of aluminium on the hydrogen embrittlement sensitivity of TWIP steels was investigated. The stacking fault energy was found not to be the most determining factor. The resistance to intergranular fracture was put forward as the main reason for the reduced embrittlement in the presence of aluminium.
Interesting papers:
- 10.5006/2959
- 10.1016/j.matchar.2019.109843
- 10.1016/j.msea.2020.140079
- 10.1016/j.actamat.2019.12.055
- 10.1016/j.tafmec.2021.102952
Hydrogen permeation in steels (finished project)
Emilie Van den Eeckhout, in cooperation with VUB and SIM (Concluded, interesting papers can be found at the end of this section)
Hydrogen diffusion is one of the main parameters controlling hydrogen embrittlement. Therefore, in this study, the diffusivity of hydrogen was investigated. The technique, based on the permeation cell of Devanathan and Stachurski, allows us to calculate the hydrogen diffusion coefficient.
A schematic representation of the permeation set-up is given below. Materials having different microstructures are evaluated in order to correlate the microstructural features with the hydrogen diffusivity.
In the second part of this research the hydrogen diffusivity in a material subjected to a constant tensile load was examined. Special equipment is added to the permeation cell so that a constant load can be applied during the test. In this case, the influence of stresses on the hydrogen diffusion through the microstructure was investigated.
Interesting papers:
Hydrogen cracks in steels (finished project)
Aurélie Laureys (Concluded, interesting papers can be found at the end of this section)
In this work, different aspects of the hydrogen induced cracking phenomenon were studied. First, an extensive assessment of the hydrogen induced cracking behavior of an industrial high strength steel, i.e. TRIP steel (a complex multiphase material), was carried out.
Hydrogen induced crack formation at notch in tensile tested TRIP-steel
Second, a more fundamental investigation of hydrogen induced cracking was performed on pure iron. Advanced characterization techniques allow to assess the crack initiation and propagation mechanisms occurring during hydrogen induced cracking.
Hydrogen induced crack in deformed pure iron studied by EBSD
Third, the effect of carbide particle addition to a simple ferritic matrix was investigated. Introducing such particles should reduce the hydrogen embrittlement susceptibility of materials. However, the role of such particles in the hydrogen induced cracking phenomenon has not yet been assessed and was, therefore, investigated in the current study.
Link between carbide and hydrogen induced cracks studied by EBSD
Fourth, the developed methodology and techniques are used to try and simulate real life cracks in nuclear pressure vessels. Hydrogen creates problems in the nuclear power plants of Doel and Tihange, since the presence of hydrogen flakes (hairline cracks) in the reactors jeopardizes the safety of the plants. The role of hydrogen in the possible crack propagation of the current cracks is a key issue here.
Interesting papers:
- 10.1016/j.matchar.2015.12.017
- 10.1016/j.actamat.2017.01.013
- 10.1016/j.msea.2017.02.094
- 10.1016/j.matchar.2018.06.030
- 10.1016/j.msea.2018.10.072
- 10.1016/j.engfracmech.2019.106546
Interaction between steel microstructure and hydrogen (finished project)
Tom Depover (Concluded, interesting papers can be found at the end of this section)
To start, the interaction of hydrogen (H) with advanced high strength steels was considered. The impact of H on the mechanical properties of TRIP and HSLA steel was evaluated by in-situ H tensile tests on notched tensile specimens. The corresponding results on both H charged and uncharged samples are presented in the figure below. A high hydrogen embrittlement (HE) degree of 60% was measured for TRIP, while only 8% of ductility loss was found for HSLA. This was correlated to the presence of Nb- and Ti-based precipitates, providing effective trapping sites for H, in this way decreasing the H diffusivity.
Stress-strain curves for TRIP (a) and HSLA (b).
A fractography study indeed proved that the brittle H induced features were present over a distance equivalent to the distance H can diffuse during the test (cf. the figure below). Comparison between the outcomes of the charged and uncharged tests allowed to visualize the effective H diffusion distance into the sample during the test. The distance H can diffuse at 5 mm/min was about 65 µm.
Detailed SEM image of both left (a) and right (b) side of the fracture surface of the sample tested at cross-head deformation speed of 5 mm/min without H pre-charging. The brittle zone is indicated
Then, the interaction of H with lab cast alloys was studied. The effect of carbide addition was evaluated in Fe-C-X alloys. Thermal desorption spectroscopy was done on all Fe-C-X materials for both the as-quenched (as-Q) and quenched and tempered (Q&T) condition. The TDS spectra of Fe-C-Ti in both conditions, together with their deconvoluted peaks, are presented in the figure below. Considering the as-Q condition, only one peak was observed showing activation energies of about 27 – 30 kJ/mol. This first peak was therefore attributed to H trapped by martensitic lath boundaries. When considering the Q&T condition; the additional peaks in the spectra were attributed to the presence of small TiC which were able of trapping a high amount of H, resulting in 3 peaks with activation energies in the range of 50-71 kJ/mol.
TDS curves of Fe-C-Ti (alloy B) in the as-Q and Q&T condition (heating rate: 600°C/h)
Three different types of H were determined, i.e. total H amount (by melt extraction), diffusible H content (by hot extraction) and mobile H content (the hydrogen lost during a 1 hour vacuum treatment; calculated by subtracting the TDS-curve with 1 hour vacuum from the TDS-curve without 1 hour vacuum, i.e. direct charging). This mobile H is correlated to H trapped at dislocations. The relation between these different types of H and the degree of HE is plotted (cf. part (a) of the figure below). For this purpose, alloy A, B and C for each Fe-C-X grade in the as-Q and Q&T condition was included (30 materials). The correlation improved for total over diffusible to mobile H. Moreover, when Fe-C-V alloys were excluded, since they did not show a significant plastic deformation, (cf. part (b) of the figure below), a R² of 95% between the degree of HE and the amount of mobile H was achieved. This clearly indicated the crucial role of H trapped by dislocations which is linked to the enhancement of the dislocation mobility by the presence of H as proposed by the HELP mechanism.
Degree of HE vs. total, diffusible and mobile H content for Fe-C-X– alloy A, B and C in the as-Q and Q&T condition (a). The Fe-C-V alloys were excluded in (b) to illustrate the correlation between mobile H and HE for alloys which failed past the macroscopic yield strength.
Interesting papers: